In today’s fast-paced world, everything in production is in constant motion, from machines and materials to people. Modern production and logistics environments rely heavily on Location-Based Process Optimization to ensure a smooth flow of materials, both indoors and outdoors. While GPS has long dominated outdoor tracking, indoor spaces are on the cusp of transformation.
Advanced sensor technologies and IoT solutions now allow organizations to observe and optimize each stage of production and logistics. However, production processes are susceptible to disruptions caused by errors or delays, making it challenging to pinpoint and address root issues efficiently.
This raises an essential question: how can companies optimize production processes for a more resilient future? It’s clear that Location-Based Process Optimization not only increases efficiency but also strengthens competitive advantages by enabling real-time, data-driven improvements.
In this article, we explore the intricacies of material flow and how Location-Based Process Optimization through automated processes can help organizations achieve more sustainable, efficient production and transportation.
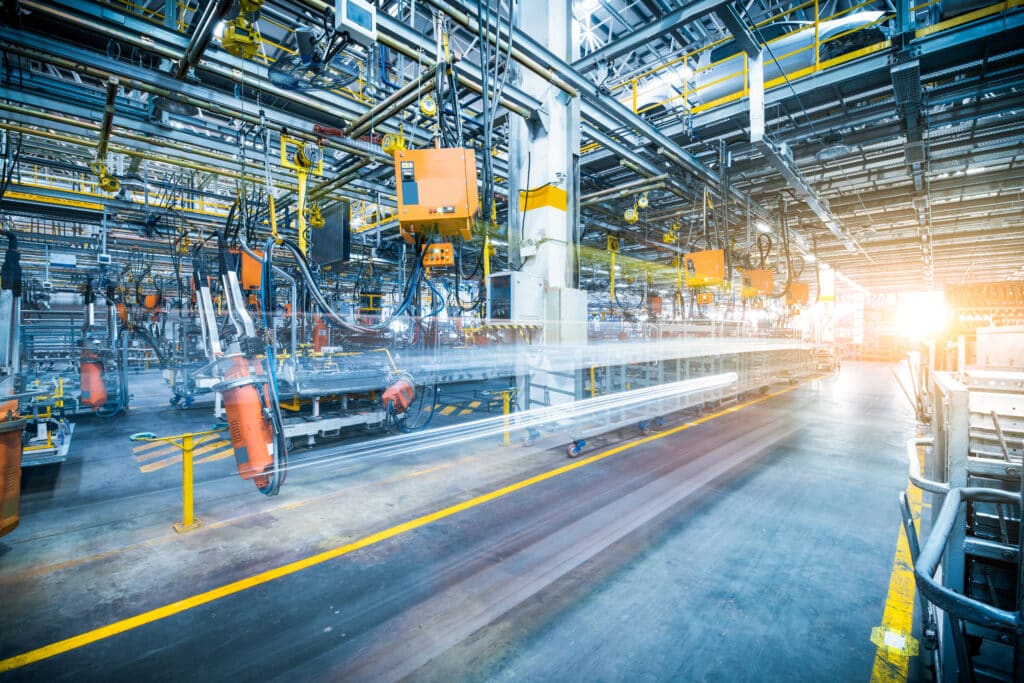
What is Material Flow?
Material flow refers to the process of storing, packaging, and moving goods. It represents the chain of logistics from the supplier to the customer; materials enter a production facility and move to assembly, packaging, quality control, and shipment.
Throughout this journey, a variety of processes are involved that increase the potential for error with complexity. Even minor issues or mistakes at this scale can lead to costly delays for everyone involved. It is therefore crucial to identify and analyze material flow in real-time, so that companies can quickly detect errors and take immediate action to eliminate inefficiencies.
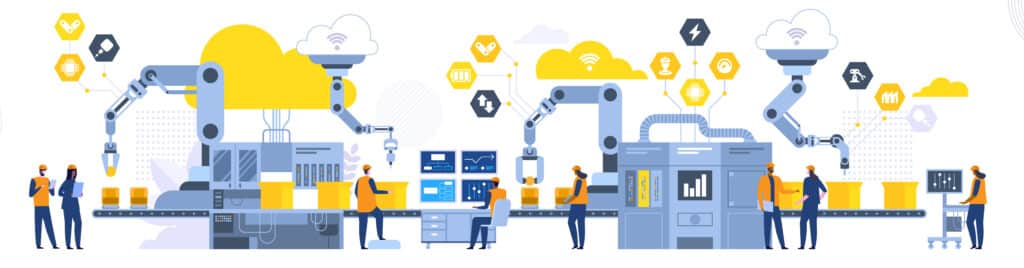
Challenges in Production and the Need for Location-Based Process Optimization
Changes in consumer patterns and globalization are two major external factors that affect material flow. Consumers are increasingly utilizing digital channels and e-commerce services. Trends change rapidly, and keeping up with these shifts can be challenging. For example, throughout the COVID-19 pandemic, we have observed how global supply chains and outsourcing have led to significant delays in the flow of materials, resulting in higher costs due to idle time or even downtime.
This is why having efficient end-to-end material flow visibility can significantly enhance organizations’ competitive positioning. It can be challenging to control operations in complex logistic or production environments without real-time visibility into material flow. Real-time location data is without a doubt the single most important tool to provide this level of visibility. Its use is therefore a central issue in the strategy for ensuring market and competitive strength.
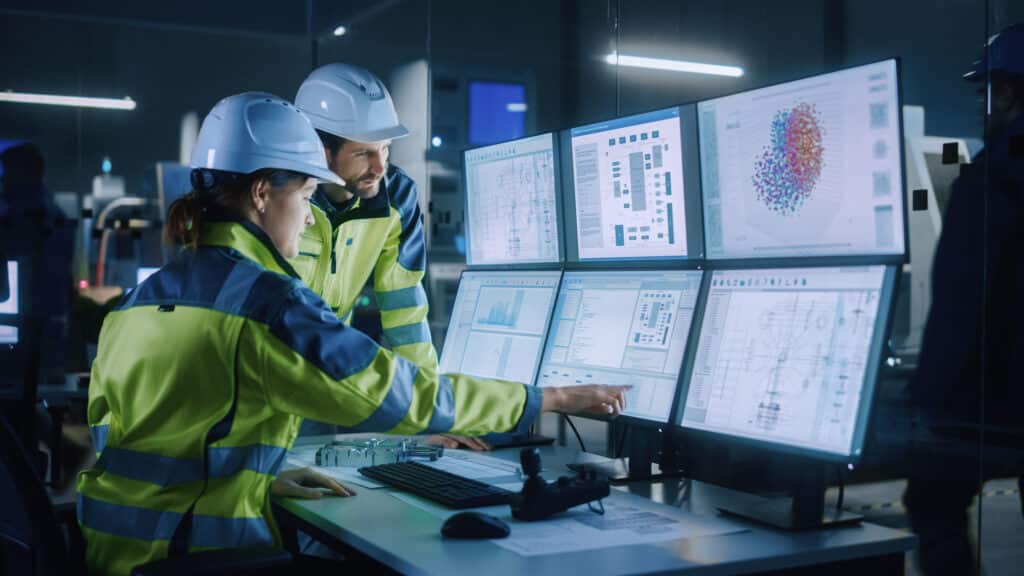
Why are Real-Time Locating Systems the Answer?
Through the strategic use of location data, organizations get valuable insights on what is happening at all stages of production, logistics and the entire supply chain. Obtaining information on the time required to complete certain tasks would require stopping at every asset movement in the assembly line or warehouse, which is hard to do efficiently without automated monitoring via a real-time locating system (RTLS).
RTLS are used to automatically identify and track the location of objects or people in real-time, usually within a building or other contained area. RTLS can provide critical information such as how many items or assets have passed through a specific assembly line without having to manually count the throughput of each item in each process step.
Managing logistics effectively is more of a guessing game than an intelligent and efficient process without real-time data. The ability to collect and analyze data from all aspects of your company’s operations is one of the most valuable aspects of RTLS. However, in order for RTLS to succeed, it is critical to decide how to use the data to drive improvement. It is one thing to gather data, but it is another to interpret it and turn it into real business gains.
Geofencing as a Tool for Location-Based Process Optimization
Even though more and more processes are being automated, many process steps still involve simple but necessary manual procedures. These manual procedures are error-prone by nature and getting rid of these is key to digitizing processes and minimizing the level of errors.
Geofences can be an effective tool to achieve this. Geofencing is a location-based service that triggers an action when an asset enters or exits a spatially-defined location. As such, an event can be set to trigger a pre-programmed action when a mobile asset equipped with a location tag enters or exits a virtual boundary set up around a geographical location, known as a geofence. Geofences can be used to define process steps in a way that assets entering or leaving a dedicated geofence automatically trigger processes, thereby eliminating manual steps.
For example, fence enter and exit events can be used to trigger an action in a Manufacturing Execution System (MES), which track the different production steps during manufacturing. An MES shows the state of parts during production and through geofence events, it can be notified when one step is completed and the next step has begun. For example, just-in-time productions could be implemented in a targeted manner. It’s all a question of location data management.
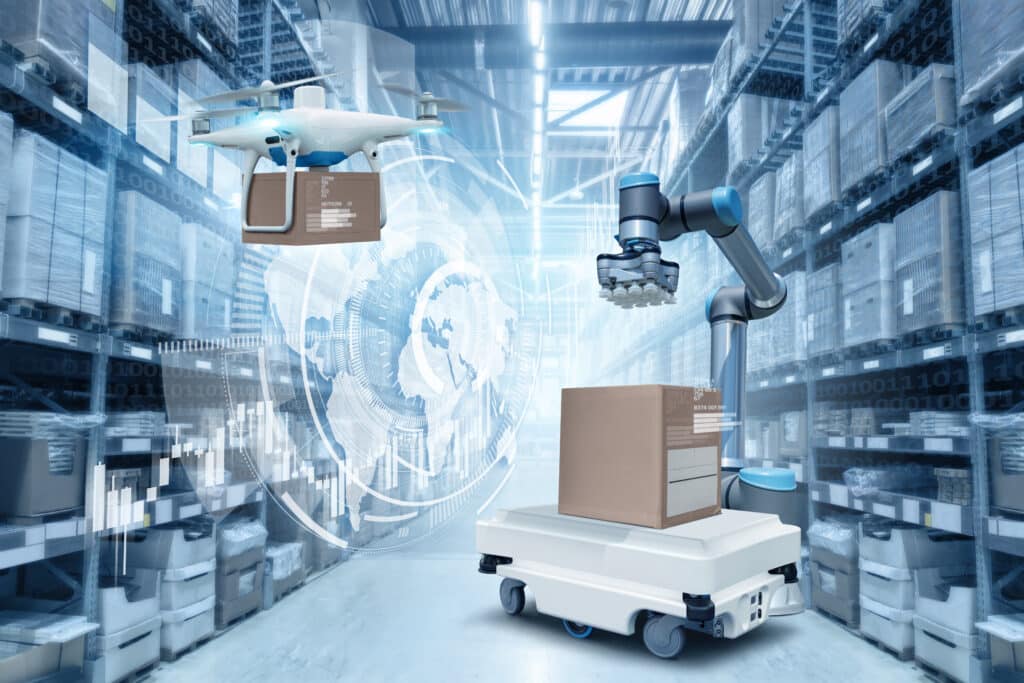
Effective Location Data Management for Location-Based Process Optimization
In order to effectively manage location data attributed to material flow, the data needs to be streamlined, and all technological components need to work together harmoniously. Our DeepHub provides this out-of-the-box. Based on omlox, the open locating standard, the DeepHub is a lightweight, high performance middleware that aggregates and standardizes location data from any location technology.
The intuitive and powerful geofencing capabilities of the DeepHub enable location-based process automation in material flow. Users can receive notifications informing them of the movement of materials, shedding light on how long each process step takes, where bottlenecks exist, and ultimately – where improvements need to be made.
The scope with which the DeepHub can be used to automate processes is practically endless. It doesn’t matter which locating technology is used or the complexity of the use case – the DeepHub can be utilized with any technology from any vendor; anywhere a location update happens, relevant actions can be triggered. This all happens within a sleek dashboard that shows the movement of assets and the triggering of relevant events in real-time.
Interested to learn more? Get in touch with us now!